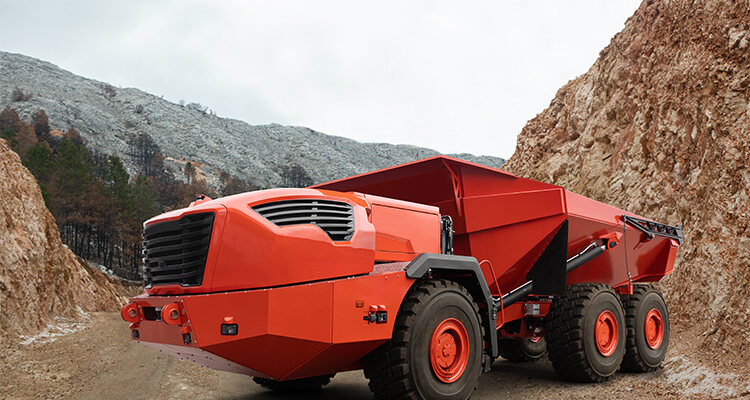
Applying the four Ds of robotization to real-world mining automation
Industry 4.0, IIoT, AI and machine learning are all terms now synonymous with industrial automation. Likewise, commentators have given much thought in recent years around the ‘four Ds of robotization: dull, dirty, dangerous and dear.’ In fact, ‘difficult’ and ‘demeaning’ have also been thrown into the mix.
But what about ‘dynamic?’ A term that focuses more on a robot’s ability to perform better than us mere humans, rather than simply picking up the more mundane, or risky, tasks.
Here, Sam Wood, Industrial Automation Product Manager for Oxfordshire-based Navtech Radar, argues that industrial automation isn’t just about robots picking up tasks that don’t require human reason or decision-making. So dynamic are the technological advancements in mining that radar technology can be deployed to help manage ever more demanding tasks, in turn improving efficiencies, reducing downtime and reducing the risk of injury.
It’s taken for granted nowadays that our lives, both in the workplace and at home, have been improved immeasurably through automation. GPS can guide us from Land’s End to John O’Groats without a glitch. A car on the assembly line can be completed to a customer’s precise specification by keying in the design requirements before a single rivet has been punched. And we’ve all been told how our smartphones today have more processing power than was available to the entire NASA team when Neil Armstrong was sent to the moon.
In extreme working environments, however, where heavy plant and machinery meet dust, obfuscation and harsh weather conditions, industrial automation is cutting through the robot rhetoric and delivering extraordinary results.
So, what are the challenges?
Let’s start with those four Ds. Mining environments are invariably dirty, and by their nature dangerous too. According to the International Council on Mining and Metals (ICMM) ‘Safety Performance Report: Benchmarking progress of ICMM company members in 2021,’ 43 people from ICMM member companies lost their lives at work. This is slightly down on the 44 in 2020 and an even greater drop from the 287 deaths in 2019 – albeit that included the 250 fatalities in Brazil when the Brumadinho Tailings Dam collapsed. An objective of the ICMM and doubtless all other organizations like it is to achieve ‘zero harm.’ Gone are the days of picks and hammers; modern mining operations deploy some of the largest plant and automation systems on the planet.
Replacing the number of human operators with machine-automated processes and equipment should take us a step closer towards our objective, reducing the field of risk and injury. But it’s not as simple as that. Much of the automation in mining happens above ground, with autonomous mining trucks (AMTs) and other plant traversing cluttered and hazardously dusty terrain. In fact, above-ground operations provide a whole new set of challenges on their own.
Where are the technological glitches?
AMTs rely upon data, deploying a multitude of sensors to navigate their terrain, without any human intervention, as they make their way along mine haul roads. Data is processed to calculate set numbers of maneuvers, such as determining speed of travel around nearby machinery and equipment, all leading to potential decisions needing to be made by onboard software. Likewise, the exact location of each AMT is tracked, with data shared via wireless networks and GPS, working in tandem with onboard obstacle detection and avoidance systems.
If this complex network of information and vehicle systems is to operate effectively, it is vital that the sensors deployed are capable of operating at the highest levels of situational awareness, so that every possible hazard is identified at the earliest opportunity. How, therefore, is it possible to be at our most dynamic when sensors can’t see optimally underground, nor at night-time nor in extremely dusty environments? AMTs need to work 24/7/365. That’s where radar comes into its own.
Radar provides reliable performance even in the most adverse conditions, including rain, fog, dust, and dirt – even when other sensors fail. Moreover, high-resolution, 360°, long-range radar builds a data-rich picture of its surroundings, working far beyond the limits of a person’s line of sight. Radar sees what humans can’t, adding that vital extra layer of safety to challenging environments.
Navtech Radar’s sensors are fully compatible with the open-source Robotic Operating System (ROS), quick to integrate, and give full access to the radar’s raw data. Radar works through extreme sunlight as well as through ‘blind spots’ where GPS can’t, meaning that assets can be tracked in literally all conceivable conditions. Moreover, radar-based solutions can be seamlessly integrated with LiDAR and GPS to deliver multi-sensor fusion applications at mine sites.
So, what else might be at play here?
No mine site should have a single point of failure, and the reliance upon implementing just one sensor-based technology for autonomous operation is a huge risk, with the potential for costly downtime, or impacts on personnel safety, as a result.
One of the greatest threats right now to GPS is ‘jamming,’ or ‘spoofing,’ where a frequency-transmitting device can be used to block or interfere with radio communications. Equally, GPS denied environments need redundancy, should there be no line-of-sight, quite often an issue in mining environments because of natural geometry or infrastructure.
To compound this, there is the ever-looming threat of solar excitation events, which can seriously degrade the performance and accuracy of any Global Navigation Satellite System (GNSS). This problem is well known to space scientists, with the effects being seen more often by satellite operators than those of a more terrestrial nature. While satellite technology takes account of the harsh operating environment of space, major events inevitably have an effect. GNSS outages are expected, for example, between 2024 and 2026 – with a peak anticipated in 2025 – when NASA, amongst others, have predicted the impacts this will have on technology on earth, and in space.
Navtech’s radar localization solution is achieving just that. It combines radar technology with mapping and localization software to deliver never-seen-before pinpoint, centimeter-level localization, even in the harshest conditions and environments. This can also be augmented through multi-experience mapping, combining the radar solution with world-leading autonomous vehicle software to collect the data needed to map any environment in incredible detail.
Back to those four Ds
Industrial automation in mining has come a long way, in that it is continually improving processes and production. It could be argued, however, that it has to some extent exacerbated safety procedures because we have brought in an added dimension to how we manage and track large and heavy machinery. Yes, the dull, dirty, dangerous, and dear tasks are now being performed autonomously, but progress isn’t just about completing these tasks – progress is about being dynamic.
Being more dynamic will mean using industrial automation to take us to the next level, to do what humans can’t, and to perform tasks that make mining more productive, more cost-effective, and of course more positive in their impact upon both the bottom line as well as the wellbeing and safety of operators.
For a list of the sources used in this article, please contact the editor.
www.navtechradar.com
Navtech Radar innovates with radar to deliver world-first capabilities in highways safety, critical national infrastructure security and industrial automation. Its solutions provide reliable performance in all conditions and push the boundaries of what is traditionally possible, using its unique radar technology. Navtech is a member of ITS America.