Discover how NEOL Copper Technologies is disrupting the sector with revolutionary technical lubricants
NEOL Copper Technologies (NEOL) is a hard-science company dedicated to developing and manufacturing revolutionary technical lubricants, which are better for machines, and kinder to the environment. Extensive research led NEOL to develop CuGlideTM; a groundbreaking copper filming technology that eliminates hydrogen wear. Rather than allowing uncontrolled hydrogen invasion of the friction surface, NEOL’s additive technology first uses its properties to polish the friction surface at the elementary level, then terminates the hydrogen wear with copper ions.
The company develops, tests, and produces lubricants with exceptional anti-wear properties that are free from harmful sulphated ash, phosphorus, and sulfur (no-SAPS). From commercial vehicles and industrial plants to railway and mining operations, NEOL provides no-SAPS alternatives for numerous applications. The company is focused on driving transformation in the conservative global lubricants industry which has existed, largely unchanged in a way it approached the issue of wear, for over a century.
“I got into the industry by circumstance really,” begins Leyla Alieva, CEO and co-founder of NEOL. “One day my co-founder asked me to join forces with the CuGlideTM technology developer, whose expertise lies in engineering and tribology, and who needed support on the business side. So, that’s basically where I came in with my financial and business development background and I think we make a great team. We’re currently focused on trying to raise awareness surrounding the technology. As it’s relatively new, we’re talking a lot about the underlying scientific discoveries (dating 60 years back) and the possibilities thereof for our users.
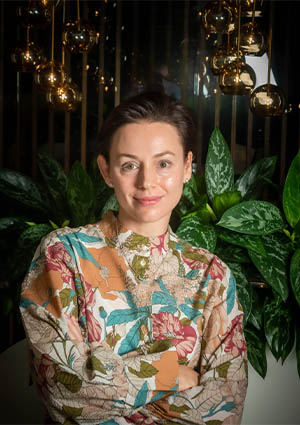
“At the same time,” she continues, “we are testing our technology and working with field test partners to showcase the effects of CuGlideTM. I’m also in the process of fundraising. We are currently in our first institutional round, having been self-funded until now. We’ve just hit that wonderful growth stage where we can no longer do it alone.
“Although we are a technology company, we’re also a lubricant developer and manufacturer. Our key competence is in developing lubricants that can preserve equipment’s moving parts. While lubricants are obviously readily available, we believe our products can significantly extend the lifetime of equipment and from what we’re seeing in our field trials, even have a rejuvenating effect on older equipment. Over time, for example, an engine will get polluted and lose fuel efficiency. We’re trying to preserve that initial efficiency level. Consider the large dump trucks used by mining companies and how much fuel they consume. Even a slight improvement can generate large savings in terms of operational expenses and emissions,” she elaborates.
“We don’t use significant amounts of copper in our products. We use copper in ionic form, which is extremely effective in forming a film over steel components to protect surfaces and bring various benefits during the lubrication process. There’s no need for any special coating procedure, retrofit or significant investment.
Powerful pilot projects
“Many of our clients appreciate the opportunity to run a pilot project first to see for themselves how the technology works. My co-founder, Dmitry Privalov, worked in metals and mining for 20 years, the last 13 of which he was based in Indonesia. As such, recent projects are in Indonesia and that’s why our current small manufacturing base is also there. We trialed a full cycle of 500 motor hours on dump trucks that operated on an open cast mine and the results were significant. There was more than a ten percent reduction in fuel consumption, a reduction in oil usage that signifies enhanced engine health as well as an increase in productivity in terms of slightly higher operational speed,” Leyla elaborates.
Indeed, the lifetime of equipment is enhanced by as much as two-to-four times. Users experience an average ten percent fuel economy improvement. There is a substantial decrease in lubricant consumption and 25-to-70 percent fewer residual hydrocarbons in exhaust.
“Maintenance engineers are generally more open to trying a new product when they have an unresolved issue,” she continues. “If they’re happy with their current product, there’s very little chance that they will want to change. Our products offer an effective solution, and once tried and tested, we tend to build trust and clients are more willing to consider additional applications.
“The impact we have on our clients’ operations can also be significant from a sustainability perspective. Our technology enables them to enhance their sustainability performance at no extra cost. Companies don’t need to change their processes or equipment to implement our products. Simply switching the lubricant can result in emissions reductions. When equipment runs for longer, it requires replacement less frequently, which conserves resources.”
Sustainability at no extra cost
NEOL’s proprietary additive package uses organic copper salts instead of toxic phosphorus and sulfur compounds. This unique composition doesn’t acidify and, therefore, doesn’t require a high base content or generate excessive amounts of sulphated ash. As a result, used NEOL oil is easily recyclable and, in some cases, fully biodegradable.
Looking to the future, Leyla shares that NEOL will continue to strive for a circular economy while expanding its operations. “We would like to share this technology with as many manufacturers as possible and showcase its benefits. While it’s not the cheapest available solution in terms of initial outlay, when you consider total cost of ownership and lifecycle benefits, it is extremely competitive,” she explains.
“It’s important to look beyond the purchase price of materials because there are optimizations to be made with new, innovative technology. Sustainability doesn’t need to come at an extra cost; today, it is very much aligned with economic efficiency. In today’s world, it’s increasingly important for humans, machines, and nature to be resourceful. While striving to achieve our own goals, we must also preserve precious resources,” Leyla concludes.
Indeed, NEOL understands the value of reserves and strives to create technologies that extend the lifespan of equipment, helping to protect both natural and human resources. Tribology is at the heart of NEOL’s product development and provides an outstanding solution to the centuries-old challenge of machine wear.