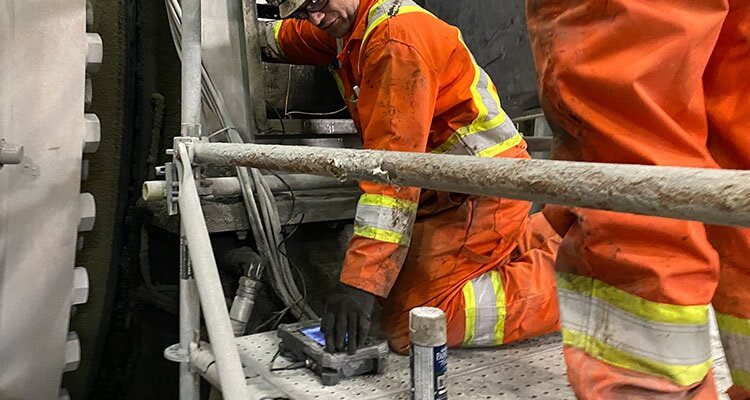
NDT in the mine processing plant: A boots-on-the-ground perspective
Co-founder and Lead Technical Consultant, Richard Malenfant, at Malenfant Technical Services (MTS), an independent third-party Non-Destructive Testing (NDT) firm servicing the mining industry, shares insights into the world of mining and processing equipment inspection as well as his experience in managing the challenges it presents in the field.
“It’s an interesting topic right now, especially because of recent changes in the industry. Precious metals and other essential raw materials (used for everything from electronics to steel and aggregates) are increasingly in demand. In the case of copper, for example, the global demand is projected to exceed the current supply capacity by 2050. New mines will need to be commissioned just to keep up with the growing demands, and existing mines will need to do everything they can to extend the life and capacity of their current extraction and processing assets.
“A universal priority for mining businesses is the management of operation risks to optimize production and lifespan. This is essentially the whole driver behind asset maintenance actually but, these operation risks encompass financial risks, environmental and health and safety risks, as well as production risks. My approach as a contractor is to always help reduce risk in all these areas through our services.
“New continuous-monitoring technologies with remote IoT connectivity and automated alarm capabilities are already rendering preventative maintenance more efficient, reliable and precise. Techniques like vibration analysis, thermal imaging and wireless bolt-tightness monitoring are minimizing guesswork in maintenance planning and execution. From an optimistic perspective, the mining industry is headed into a new technological revolution of asset management. A futuristic vision comes to mind of seamless connectivity and automation leading to a scenario where human operator error is entirely phased out. Perhaps, even someday an entire process plant with AI asset management could prevent its own mechanical failures and operate nearly autonomously. However, we are not there yet.”
The reality is and will remain that eventually, everything breaks. Inevitable imperfections plague the efficiency of complex, interconnected systems that are regularly pushed over capacity. Improper installation, poorly executed modifications, misalignments, and load and torque errors catalyze failures. In the end, fatigue, corrosion and wear destroy all machines and this fate costs mines and their investors greatly each year. These risks and realities are mitigated by slowing deterioration with condition monitoring, evaluation and trending analysis.
New advances in NDT boast remarkable inspection capabilities. The result of these NDT innovations is significant time savings, cost-reduction and environmental and safety risk mitigation for their clients. For example: MTS’s girth gear teeth inspection by Eddy Current Array detects fatigue cracking without the need to clean greased gear teeth. Pulsed Eddy Current technology offers corrosion detection even through tank and pipe insulation and jacketing. MTS doesn’t limit itself to using the latest in NDT technologies though. It has also adopted other performance enhancing innovations, like Sena Technologies’ latest over-the-ear hearing protection with integrated communication systems, Cast. MTS technicians and leadership especially rely on Sena’s Cast headsets to communicate in high-noise environments when process plants are only partially shut down. According to research conducted at Lund University (Sweden), worker down time is reduced by over 50 percent when using hearing PPE with integrated communication systems.
When asked to comment further on the topic of health and safety risks in the process plant shutdown environment, Richard adds: “Any responsible member of the mining community will tell you that the priority is always safety; in our case, we take it up an extra notch; ’safety first, safety second and safety third’ is our safety moto. Working around or within large rotating equipment, around pinch points and close to other contractors performing welding and lancing for instance has taught us that above all else communication is the best defense against incidents. These forms of communication start at the administrative level with policy, enter the realm of engineering controls with lock-out and Tag-out processes and finally come down to the most critical last-line of defense: line-of-sight and non-line-of-sight team communications. Someone needs to know where everyone is and what they are doing at all times on a large-scale shutdown.”
Back on the topic of NDT, Richard continues to explain the added value of the integration of NDT into the preventative maintenance plan of an asset; “One of the oldest and most effective tools in the preventative maintenance toolbox is NDT. For mining and processing assets (grinding mills, crushers, tanks, pipes, mining shovels) it offers a reliable, direct source of information for mechanical engineers, asset management professionals, risk analysts and specialized consultants who are part of overarching strategies to reduce operational risks.
“Faster, less expensive and more reliable NDT inspection technologies are helping to optimize inspection planning and budgeting. The inspection frequency of any given asset should be directly linked to its operational risks; the higher the risk, the higher the inspection frequency should be. At one mine site we work at, our team executed a successful preventative plan involving a high risk of catastrophic failure of a SAG mill ring gear. In this example, we were contracted to complete a 100 percent eddy current array scan of the gear teeth annually. This inspection cycle went on smoothly for several years without any significant findings until one year two cracks were detected. Immediately, ameliorative actions were taken, and the inspection frequency was increased to every six months to detect any new cracks. To monitor the cracks for propagation, we used phased array ultrasonic testing every one or two months. A spare gear was purchased with a 12-month lead-time. The crack growth trend showed that the teeth were holding up well enough that the mine would be able to run it long enough to plan and execute a gear change.”
Richard continues with a final statement and summary: “Annual NDT inspection is generally recommended for gears, pinions and other rotating shafts such as conveyor pulleys. Other cyclically loaded structures such as mobile equipment and lifting devices should also be inspected annually. Thickness testing on rotating equipment should be done at least every 12 or 24 months, while thickness testing on tanks and vessels is recommended at 24-to-36-month intervals. These are of course general guidelines and not applicable to all cases; each asset should be managed on a case-by-case basis. With good quality inspection data an experienced asset management consultant can provide great insight and value to a preventative maintenance plan. If good consultations are made and followed by the mine, then operating risk can be reduced.”
For a list of the sources used in this article, please contact the editor.
www.malenfantindustrial.com
Malenfant Technical Services (MTS) is an industrial services provider, specializing in 3rd Party Inspection and Non-Destructive Testing (NDT) services for mining and processing equipment and other heavy industrial assets. Despite operating primarily as a vendor for NDT, MTS offers a wide range of analytical solutions, providing more holistic services than a traditional NDT approach.
www.sena-industrial.eu
Sena Industrial is one of the world’s leaders in Bluetooth® communication devices for industrial and outdoor work environments. Its solutions are designed to address the demands of today’s industrial workers by offering more efficient, comfortable communications, better hearing protection, ease of deployment and use, and safer operation. All at a value unsurpassed in the industry.