Sealing success: The role of advanced sealing in greener mining. By Warren Smith
Mining is entering a new era – one defined by the pressing need to balance productivity with environmental responsibility. As climate impacts intensify and regulations around emissions and resource use become more rigid, mining companies are under increasing pressure to operate more sustainably. Disruptions from extreme weather events are no longer rare, making operational resilience a top priority across the sector.
While much of the industry’s focus has been on headline-grabbing advances such as automation and digital transformation, some of the most impactful progress is being made through less conspicuous innovations. Among these, advanced sealing technologies are emerging as a quiet force for change, helping mining operations achieve sustainability goals and enhance reliability.
Reducing downtime
Mining operations rely heavily on rotating equipment, and seals are critical to keeping this equipment running. However, packing sealing systems and mechanical seals are also a leading cause of slurry pump failures, especially under the punishing conditions of modern mining. High temperatures accelerate wear, while freezing conditions cause brittleness and inefficiency. When seals fail, the consequences are costly. In fact, a single failed seal can stop ore processing for eight-to-24 hours, with lost productivity and expensive repairs. Over the past five years, such failures have cost mining firms $67 billion.
Mechanical seals, however, have evolved dramatically. Innovations such as spiral groove technology, diamond-coated faces, and IoT-enabled predictive maintenance now offer a low-barrier, high-impact upgrade for mines seeking to reduce emissions and water use. According to McKinsey, leading mining operations have cut unit costs by three-to-six percent annually and increased production by up to 40 percent through operational excellence and equipment reliability. Upgrading to modern mechanical seals is one of the simplest, most energy-efficient steps a mine can take.
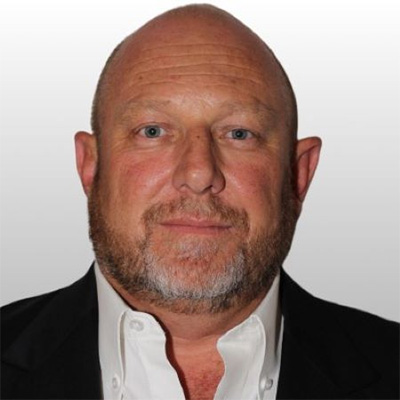
How rules and new materials are shaping sealing
The Clean Air Act and EU Industrial Emissions Directive are forcing the adoption of dual seals and gas-lubricated designs to reduce fluid leakage. In arid mining regions, water regulations have spurred the development of closed-loop seal systems that dramatically reduce water loss compared to traditional gland packing.
Recent innovations include abrasion-resistant materials like duplex steel and nickel-chrome, with laser-etched grooves for optimal lubrication and nanocrystalline diamond coatings for extreme durability. These developments allow seals to withstand the harshest slurries and climates, making them a strategic enabler of sustainable mining.
Conserving water in challenging environments
Consider a copper mine in southern Peru, operating in a water-scarce region and facing the challenge of balancing the water-intensive demands of copper extraction with the need to conserve water for local communities. Traditional gland packing systems consumed about 68 liters per minute just for cooling and lubrication. This was an unsustainable figure, especially in regions such as Chile’s Salar de Atacama where mining has already consumed over 65 percent of local water supplies.
By switching to advanced mechanical slurry seals, featuring diamond-coated faces, the mine was able to run a fully dry operation, eliminating the need for external cooling water. Since installation, the seal has performed reliably, with no reported issues. This example demonstrates that mechanical seals (once considered unsuitable for mining) are now critical to sustainable operations, offering a practical, immediate step towards decarbonization.
Achieving more with less
In Queensland’s Bowen Basin, one of Australia’s most productive coal regions, a major coal mine faced high temperatures, abrasive slurries, and mounting pressure to reduce water use. The site’s slurry transport system, operating with multiple pumps in a three-stage configuration, handled high solids content at significant pressures and temperatures over 30°C – conditions that pushed traditional seals to their limits.
By installing mechanical seals designed for high-performance slurry applications and supported by a low-pressure water line, the site significantly reduced water consumption and simplified piping. Water consumption dropped to just 6.3 liters per day, a remarkably low figure for such harsh conditions. With each seal expected to last 12–18 months, downtime and maintenance have plummeted, translating directly into cost savings and operational predictability. In similar applications, mining operations have reported water savings of up to 120 liters per minute, per pump, enabling leaner, more efficient mining.
Staying reliable in a digital world
Mechanical seals are playing a key role in bringing digital innovation to mining. With the addition of IoT sensors (either built into new equipment or retrofitted to existing pumps) these seals now provide valuable, real-time insights into how equipment is performing. Operators can track factors like pressure, temperature, and vibration as they happen, sending this data to central systems that support smarter, more targeted maintenance.
This shift is especially important given that over 80 percent of mines still lack the tools to accurately measure the true cost of downtime, often because they don’t have enough operational visibility. By retrofitting pumps and motors with sensors, maintenance teams can spot potential issues early and take action before they lead to bigger problems. This proactive approach helps reduce unexpected breakdowns and keeps equipment running longer.
The results are clear: predictive maintenance can extend the life of seals beyond the usual 12–18 months, cuts down on manual checks and gives operators more confidence and control over their operations.
Progress through practical upgrades
Achieving a more sustainable and resilient mining sector doesn’t always hinge on extensive technological overhauls or significant capital investments. Often, meaningful progress begins by re-examining the essential components that keep operations running.
Innovations in sealing technology, that are designed for longevity, efficiency, and digital connectivity, are proving to be practical tools for reducing emissions, conserving water, and strengthening operational reliability. For today’s mining operators, steady improvements in these areas can lead to significant gains.
As the industry continues to navigate the challenges of climate change and resource constraints, it’s clear that smart, targeted upgrades like advanced sealing solutions play a vital role in shaping a greener future for mining.
Currently in the role of Global Mining Market Director at John Crane, Warren Smith is an accomplished engineering and industrial leader with over three decades of global experience. Warren began his career as a Fitter and Turner before progressing through technical and managerial roles. He brings deep industry insight and a hands-on approach to problem-solving, underpinned by his technical training at Germiston Technical College and leadership cultivated over decades in the field.