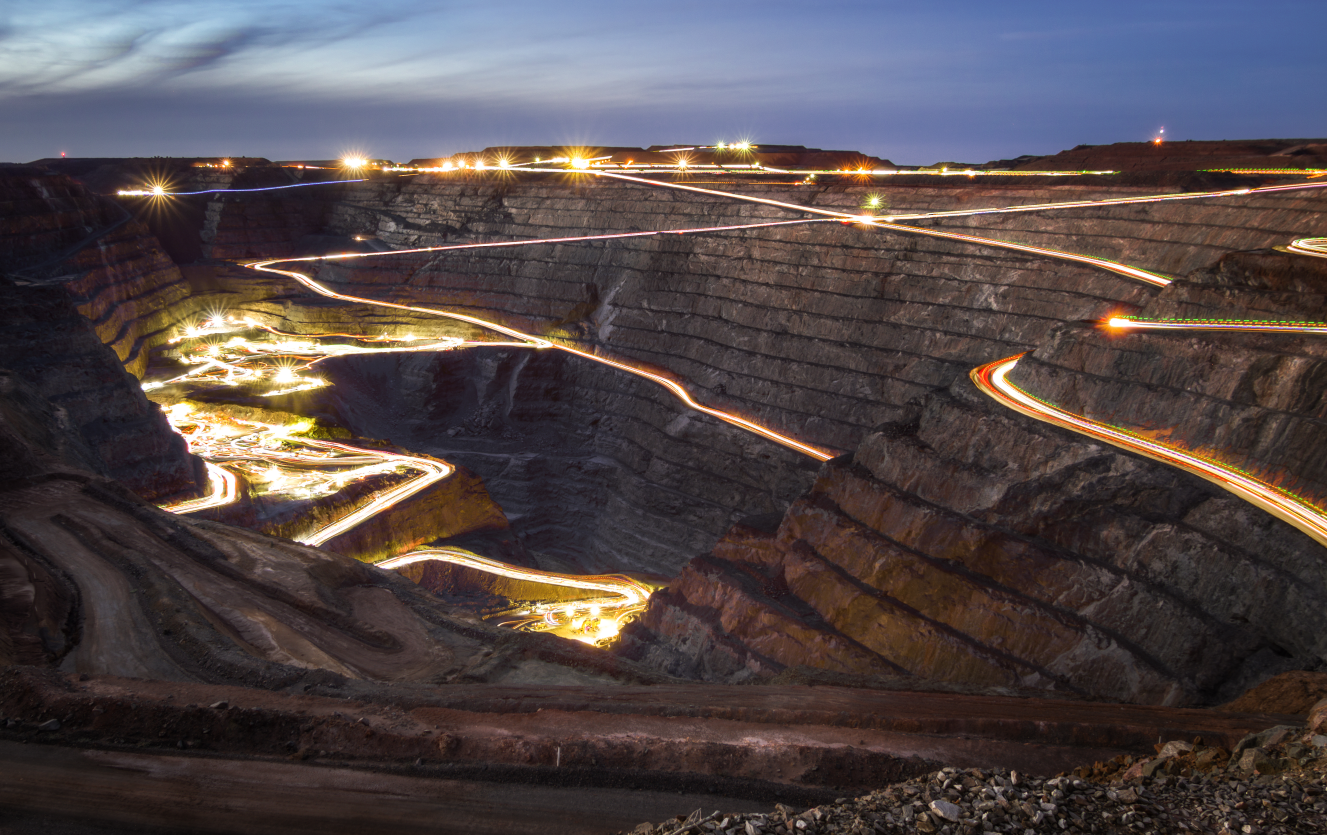
Sustainable mining, minerals, and metals operations: digitization is key. By Tara Ran
The rise in energy use is a double-edged sword; though it has contributed to substantial economic growth and a significant rise in living standards, it has also deeply impacted the environment. Industries, now operating in a world plagued by natural disasters, rising sea levels, and failing crops, are under pressure. The expectation to decrease their carbon footprint has meant that mining, minerals and metals operations are now at the forefront – for both regulators and consumers.
As energy-intensive industries, mining, minerals and metals firms may find this daunting. Fortunately, stakeholders have new means through which to lower CO2 emissions. Green energy and sustainable operations are viable solutions and are just one part of Industry 4.0 trends that are currently emerging.
Mining, minerals, and metals: Making the transition to sustainability easier
Regulatory demands, marketplace views, and a desire to reduce greenhouse gas (GHG) emissions have encouraged mining, minerals, and metals industry operators to more actively pursue options that cut energy use and assist them in becoming more sustainable industries. New off-balance-sheet financing mechanisms are helping to remove the obstacle of high up-front capital investments sometimes associated with energy efficiency initiatives. Such approaches enable companies to use the energy savings derived from the new technologies to pay for the investment over time, using the OpEx savings to fund the capital expense.
Below are four ways digital technologies can help mining, minerals, and metals industry stakeholders evolve to lower-emissions operations:
- Design optimization of power system designs – Energy systems that traditionally provide power and/or backup power to remote mining, minerals, and metals worksites often include diesel generators. Over time, diesel consumption and related maintenance drive high environmental and financial costs. To reduce these costs and lower CO2 emissions, new cleaner and more reliable alternatives are presenting themselves.
One example of such a solution is the recent partnership between Schneider Electric and Wärtsiliä to create a sustainable uninterrupted power solution for the most remote lithium mines in the world. The holistic fit-for-purpose power system includes tailored power supply consulting and design, power infrastructure build, equipment delivery, installation, digital microgrids operation, and commissioning available to mining operators worldwide. The joint solution optimizes the efficient delivery and use of energy. It unifies and leverages microgrids, thermal power generation, energy storage, and other renewable energy sources to provide a highly cost-effective power solution with a minimal environmental footprint for the mining industry in those remote areas with difficult access to energy, delivering an average 27% CapEx saving and 20% CO2 reduction.
- Modules prefabricated for E-Houses – An E-House is a pre-configured and pre-packaged modular electrical and control center enclosed in a container at the factory. The equipment residing within the module – smart transformers, uninterruptible power supplies (UPS), busways, MV switchgear, LV switchboards, variable speed drives (VSD), HVAC and control systems – are all digitally connected to enable remote monitoring. Such systems allow for much more efficient energy distribution. These self-enclosed solutions are pre-designed with sustainability and safety in mind, meet international standards and local regulations, and can be rapidly configured and delivered to accommodate aggressive project implementation timelines, as seen in Tuprag, the largest gold mine in Europe which produces 13 tonnes of gold thanks to an efficient electrical distribution system.
- An advanced asset management system – As key mining, minerals, and metals assets age, component wear leads to less efficient operations and higher instances of failure. Digital tools offer the ability to anticipate and address equipment performance issues before they become critical incidents, thereby mitigating safety risks, avoiding unplanned downtime, and the related energy-intensive and time-consuming restart procedures. It helps also extend the asset lifecycle, reducing waste.
- Power quality analysis through digitization – Cloud-based tools now can help operations managers quickly sift through power system data using advanced algorithms that offer new insights into hidden problems. Certain tools can identify issues such as poor power factor, blind spots caused by unmetered loads, transformer overcapacity, and excessive voltage harmonics. Quickly addressing these issues through a cloud-based diagnostic service lowers overall energy consumption while improving power system reliability.
Enhancing green activity yields efficiency
While digital tools improve the efficiency of electrical systems, in turn reducing energy consumption, CO2 emissions can also be significantly reduced using digital architecture. Using these architectures, mining, minerals and metals industries can quickly utilize information technology (IT) and operations technology (OT) to work across several different systems and sites. This allows the delivery of insights across information silos, ensuring that KPIs are tracked in real-time to reach maximum efficiency across the business. Business risks and core production can be monitored via on-premises, cloud, and edge solutions. Cloud-connected data can be viewed by operators at any time, at any location and from any device. Visibility and resiliency can be optimized through predictive analytics, smart alarming, and live sensor data. Operations can also access experts who monitor these connected assets at any time of day.
Energy data across multiple stages of the value chain can be analyzed and captured through other approaches such as integrated operations management. Vale, among the top five largest mining companies in the world currently implements this technology that allows data to be integrated directly into the system, so Vale’s managers have granular insights without having to manually transfer any intelligence.
Waste reduction can be achieved by preventing unnecessary stops and starts, and ensuring all processes are streamlined. As a result of this, sustainability reporting is pinpointed and direct. This view of data allows an energy consumption baseline to be established. A detailed analysis of energy performance data, energy distribution within the plant, and comparisons between facilities is possible. Analysis of energy-saving initiatives and investments can also be achieved; as well as an overall view of how this can help drive a positive impact on the environment.
Tara Rana is Global Solutions Architect – Mining, Metals & Minerals Industry at Schneider Electric. Schneider’s purpose is to empower all to make the most of energy and resources, bridging progress and sustainability for all. It calls this ‘Life Is On’. Its mission is to be your digital partner for Sustainability and Efficiency.
It drives digital transformation by integrating world-leading process and energy technologies, endpoint to cloud connecting products, controls, software and services, across the entire lifecycle, enabling integrated company management, for homes, buildings, data centres, infrastructure and industries.