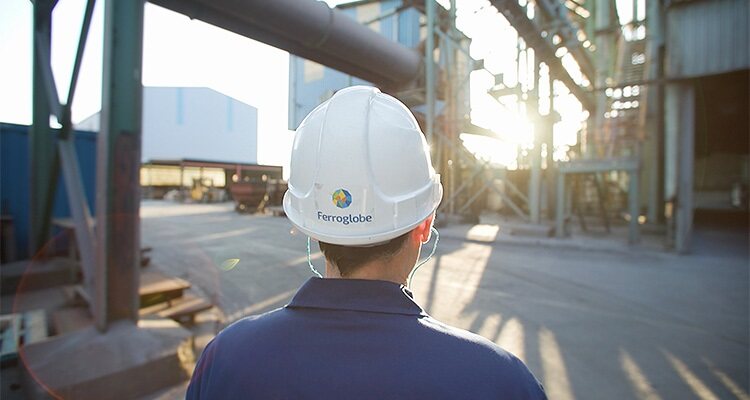
Why Ferroglobe is ensuring its future stability in light of the global energy transition
Ferroglobe is a global leader in the production of silicon metal and ferroalloys based on silicon and manganese. Listed on Nasdaq, the business has a strong workforce of around 3500 employees spread across more than 25 plants, production centers, and mining sites.
The company as it is known today was formed in 2015 through the merger of privately-owned Spanish business, Grupo Ferroatlántica, and the publicly listed US organization, Globe Specialty Metals. Despite its short history as Ferroglobe, its assets and workforce have a long history spanning over 30 years.
While the business serves customers across the globe, it has a physical presence in Spain, France, Norway, Canada, the US, Argentina, South Africa, and China. It has a unique operational footprint, vertically integrated into critical raw materials like coal and quartz.
Sustainable solutions
Its product portfolio is just as unique as its footprint. Its products serve fast-growing and dynamic sectors like solar, automotive, consumer products, construction, and energy. Driven by evolving global megatrends, such as decarbonization and electrification, the company’s levers of growth are quality, innovation, and sustainability.
“We offer a wide range of solutions, but I’ll outline some of our core lines,” begins Marco Levi, Ferroglobe’s CEO. “Firstly, we provide silicon metal, which is a crucial component in the production of numerous applications, including aluminum alloys, chemicals, semiconductors, and solar panels. We produce manganese alloys, an essential product in the steel industry, as well as silicon alloys, where we combine silicon with other elements like manganese, calcium, iron, and magnesium to confer unique properties that are valuable for customers in several industries.
“We also offer silica fume, an inorganic, amorphous silicon dioxide (SiO2), consisting of small particles collected by electric arc furnace filtration systems during the production of silicon and ferrosilicon. On top of this, we provide high-purity silicon for advanced technologies, which can be used as an active material for anodes, as a precursor in lithium-ion batteries, or used for pyrotechnical applications, alloys, and advanced ceramics.
“Our products are used by many industries for various applications,” he continues. “In the chemical industry, for instance, silicon is used to produce silicone compounds – the precursors of more refined materials – which have thousands of applications for automotive, construction, healthcare, or consumer products.
“Silicon is also a key material for photovoltaic applications and electronic semi-conductors. In this sector, metallurgical silicon must be purified into high-purity polycrystalline silicon and then further processed into mono crystalline silicon ingots, which are sliced into wafers before being processed as photovoltaic cells. A similar process is required to produce silicon chips from even higher purity silicon mono crystals and wafers before imprinting chips.
“Silicon is also used by aluminum manufacturers to improve the already-useful properties of aluminum. When used alongside aluminum, silicon provides ‘super heat’ to improve the castability, machinability, and strength of the aluminum.
“In the case of batteries, high-purity silicon is used as either an active anode material or as a precursor in lithium-ion batteries,” Marco adds. “These examples demonstrate how silicon metal has evolved into a critical material for the advancement of innovative, cost-effective, and low carbon footprint solutions to accelerate the global energy transition.”
The importance of silicon in aiding sustainable energy transition is also appreciated at a national level, with the US Department of Energy including silicon in its ‘2023 Critical Materials List’. “This recognition highlights the pivotal role of silicon in shaping a sustainable future, reaffirming its value as a strategic component in meeting increasing demands for electric mobility batteries and solar energy technologies.
“There are other policies that have had a positive impact on our business too, such as the Chips Act, the Inflation Reduction Act, and a recent bipartisan bill to enact a 35 percent tariff on imports of Russian and Belarussian ferrosilicon with the aim of instead stimulating US-based production. Such legislative actions aimed at protecting and nurturing domestic production favorably impact our business and paint a bright, prosperous future for Ferroglobe in the US.”
Evolution and innovation
With the future in mind, Ferroglobe is thinking ahead to integrate its supply chain and maintain its strong position in shaping the energy transition. “Considering our role in silicon metal supply across the globe but particularly in the US, combined with the growth potential of the solar and advanced battery markets, we’ve established a long-term strategy to be back integrated in quartz, the critical material required to produce silicon metal,” Marco explains.
“We’ve recently acquired a high-purity quartz mine in South Carolina, which will boost our annual production capacity to more than 300 kilotons of quartz. It will also increase our mining capacity by 50 percent when combined with our existing quartz operations in Alabama. The acquisition enables us to better control our supply chain, ensuring that we can access a dependable supply of high-purity quartz and eliminating the need to rely on third-party suppliers.”
Ferroglobe’s operations are guided by the principle of constant evolution and innovation. “We’re currently working on the development of a new silicon-dominant anode technology using advanced micrometer silicon,” Marco reveals. “We expect to start commercialization of the process at the end of this decade, with plans ongoing to supply the anode material directly to the battery cell producer.
“In terms of energy, we are aware of the importance of guaranteeing the future sustainability of our plants. We have recently signed a long-term Power Purchase Agreement (PPA) for the supply of renewable energy to our production plants to reduce not only our own carbon footprint, but also the credentials of the final product.”
Turning to the future, Marco reflects: “Industries around the globe have battled the challenges of the pandemic, global conflict, and volatile energy prices over the last few years, and such uncertainty is likely to continue into 2024. At Ferroglobe, we launched a transformation plan in 2020 to improve our overall efficiency, increase productivity, and reduce costs.
“We will continue to evaluate our operating practices to adjust capacity in line with demand changes and will consider relocating production to areas with lower costs if necessary. We will also continue the process of optimization in key areas like working capital, commercial excellence, and procurement, with the aim of advancing through our value creation program to become a best-in-class organization.
“Our investment into growing our silicon metal power project for batteries and other advanced technologies will also continue as we look to identify new strategic partnerships within the industry. Given the huge growth potential of this project for markets like solar and electric mobility, we hope to position ourselves as one of the key suppliers of high-purity silicon metal.
“To do so, we must focus on growth, regain our competitiveness, and consolidate our operations,” Marco concludes. “Overall, Ferroglobe’s main ambition is to lead the silicon metal and alloys-based production in the western world and strive for our economic activity to positively contribute to building a more sustainable world for the future.”